Honda Fires Up First Megacasting Plant
For its future Fully Electric Vehicles Honda has engineered something called "Intelligent Power Unit" (IPU). This IPU is a lightweight and thin new battery pack architecture which uses a die cast battery tray instead of one made with stamped sheets, reducing the number of components and integrating more parts into one or two pieces.
Honda estimates this platform will reduce costs by 40% at the pack level and reduce the number of parts from 60 to just 5.
In Ohio, USA, Honda renovated the Anna Engine Plant (AEP) to accomodate six Carat 610, manufactured by BühlerPrince in Michigan. The renovation of the Honda engine plant into a megacasting plant is part of a massive investment from Honda to build a new EV hub in the United States. Other investments include EV assembly lines and a battery cells manufacturing facility in partnership with LG Chem.
This week’s official announcement; Six >6,000t die casting machines in Ohio are test producing the battery tray halves which make up the IPU. The dimension of the parts will vary depending on the size of the vehicle and the two halves will be joined together using Friction Stir Welding (FSW).
Here are more details officially revealed by Honda this week.
• Six 6,000t machines installed which Megacast the IPU battery case in Ohio. The battery case is much larger than anything Honda has die cast before and is made in two halves.
• The battery tray halves are produced in two different sizes for midsize and large EVs – with one-half of the case common to each size.
• Honda is recycling 100% of the scrap aluminum from the process to be reused in-house.
• AEP is using Friction Stir Welding FSW to join the two halves of the aluminum battery case, using an environmentally responsible method to produce high-strength welds that reduces the amount of energy required for welding.
• To quickly and accurately visually analyze the quality of each battery case, AEP will employ a new multi-camera machine to perform Photogrammetry.
• AEP will use Photogrammetry systems in two locations to achieve 100% quality confirmation. 1) Following the die-cast process, four machines equipped with 90 cameras will visually analyze the part shape to ensure 100% quality of the surface of the battery case surface. 2) After final assembly and prior to shipping of the case to the Marysville Auto Plant, two machines equipped with 120 cameras will visually analyze each case to ensure mountability of the case to the vehicle frame.
What about Underbody Gigacastings?
Honda announced that they are planning to use Front (FUB) and Rear Underbody (RUB) Gigacastings on their future vehicles but not until 2028. Honda will invest in a new manufacturing facility in Alliston, Ontario, with a capacity of 240,000 EVs per year in 2028. These vehicles will adopt FUB and RUB single piece castings.
US OEM Plans to Deploy US-Made Magnesium in Future Vehicles
Magrathea, a company developing innovative technology for the production of carbon neutral light metal from seawater, has partnered with a multinational automotive manufacturing company to deploy US-made magnesium in current and future vehicle products.
Under the terms of the partnership, the automaker has pre-purchased a percentage of Magrathea’s future demonstration plant product. In collaboration with key stakeholders, the automaker will qualify the metal, alloy it, and incorporate it into existing products at US-based manufacturing facilities.
“This partnership is a clear signal that top-tier industrial players see the strategic importance of our product” said Alex Grant, CEO of Magrathea. “We're scaling a technology that delivers a secure, clean alternative to Chinese Pidgeon process magnesium at a time when both supply chain resilience and deep decarbonization are global priorities”
Magrathea’s automaker partner already uses magnesium across multiple vehicle brands and is a leader in advanced manufacturing technologies such as thixomolding. Today, their vehicles contain an average of 5kg of magnesium each, with potential to scale to 20-40kg per vehicle in the near future.
Beyond the automotive sector, Magrathea has secured LOIs and MOUs from leading North American, South American, and European magnesium buyers representing over 25% of the world’s ex-China demand for the metal. These partners include primary and secondary aluminum producers, metallothermic reduction operators, powder producers, desulfurization product distributors, sand casters, and die casters.
After Tesla, Toyota Becomes the First OEM to Fully Own a Factory in China
Toyota has announced that Lexus will establish a wholly-owned production facility for pure electric vehicles in Shanghai, with an initial annual production capacity of 100,000 vehicles and a workforce of 1,000 employees. Production is expected to commence in 2027.
A few months ago, Toyota revealed that the Lexus LF-ZC would enter production in 2026, employing the unboxed manufacturing process along with Front & Rear underbody Gigacastings, just like Tesla's approach.
If the Lexus LF-ZC is also to be manufactured in China, I expect that Toyota will adopt Gigacasting technology in Shanghai, mirroring the new methods at its Japanese facilities.
With this new factory, Lexus becomes only the second foreign automaker to fully own its production site in China after Tesla, marking the first instance where a Japanese car brand has deviated from the traditional joint venture model in the country.
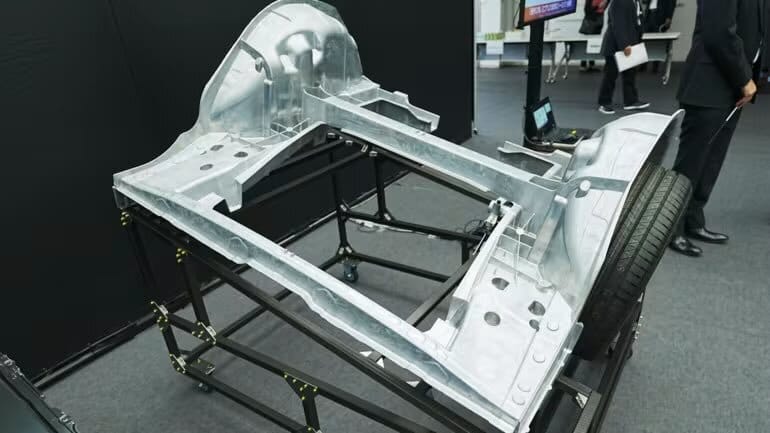
Toyota Rear Underbody Gigacasting
GISSCO Giga Semi-Solid Slurry Making Machine
Jess Wannasin, GISSCO’s CEO announced a “major breakthrough” for the die casting industry, in fact GISSCO was able to produce a 60 kg aluminum semi solid slurry with their new Giss unit designed for Giga Press size die casting machines.
We are pushing the boundaries of GISS Technology with a new GISS unit designed to prepare slurry and semi-solid metal for GIGA die casting machines.
Today, we successfully produced a 60-kg aluminum “cake,” demonstrating our slurry formation capability.
Next up? Scaling to 100 kg and beyond!
This marks a significant step toward enabling GIGA casting applications with semi-solid metal technology.
Additional information was revealed:
It takes approximately 5-10 seconds of GISS processing to create a superheated slurry for Gigacasting, which is performed during the die dwell and spray time. By using GISS, the cycle time of the Gigacasting process can be reduced due to faster solidification. We are currently conducting a slug-cutting test to demonstrate that the superheated slurry can consistently produce a uniform SSM structure. (The waiting time to get to 50% solid fraction is indeed longer than 90 seconds due to the massive heat content of big volume)
Linamar Sells its Gigacasting Plant
Canadian auto parts manufacturer Linamar Corp. is seeking to sell or lease the property of its new production facility in Welland, Ontario, Canada.
The production facility was originally intended to manufacture Rear UnderBody (RUB) Gigacastings for a well-known, North American OEM.
Linamar was initially set to install three 6,100t Bühler die casting machines and planned to be operational by Q1 2025. It remains unclear whether all the die-casting machines have been installed or if they are included in the sale. In my opinion, they are not.
I understand that the American OEM intended to use the RUB Gigacastings for its electric vehicles; however, its aggressive electrification plans have been scaled back due to revised, less optimistic forecasts for the EV market in North America.
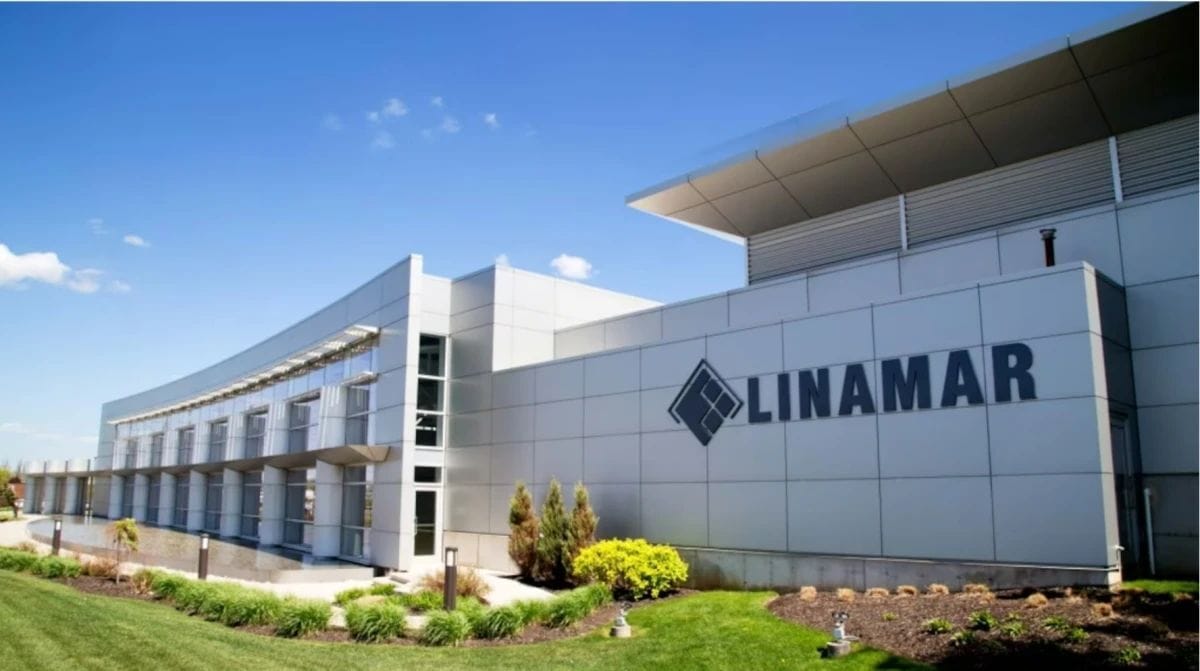
Wencan Quick Update
Wencan’s New Facility in Chongqing, China is set to be completed by the end of June 2025. It will house two 12,000-ton Giga Presses manufactured by LK Machinery.
Wencan is not new to the Gigacasting market and has substantial experience with former Huawei's brand, AITO, among others. In fact, Wencan operates several die casting machines ranging from 6,000 to 9,800 tons in various facilities. For instance, at the Seres factory, they produce RUB gigacastings, as well as FUB and side panel megacastings for the AITO M9.
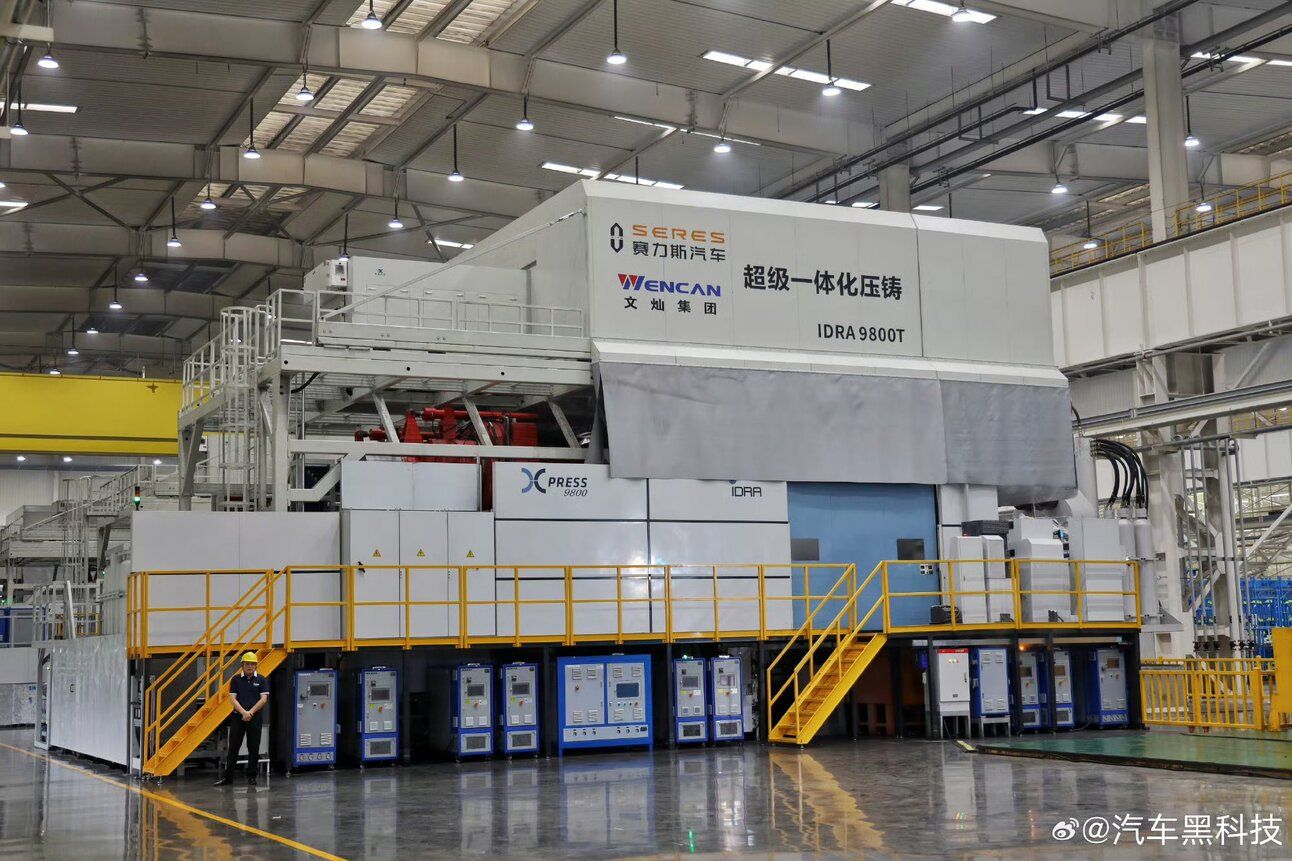
Gallery
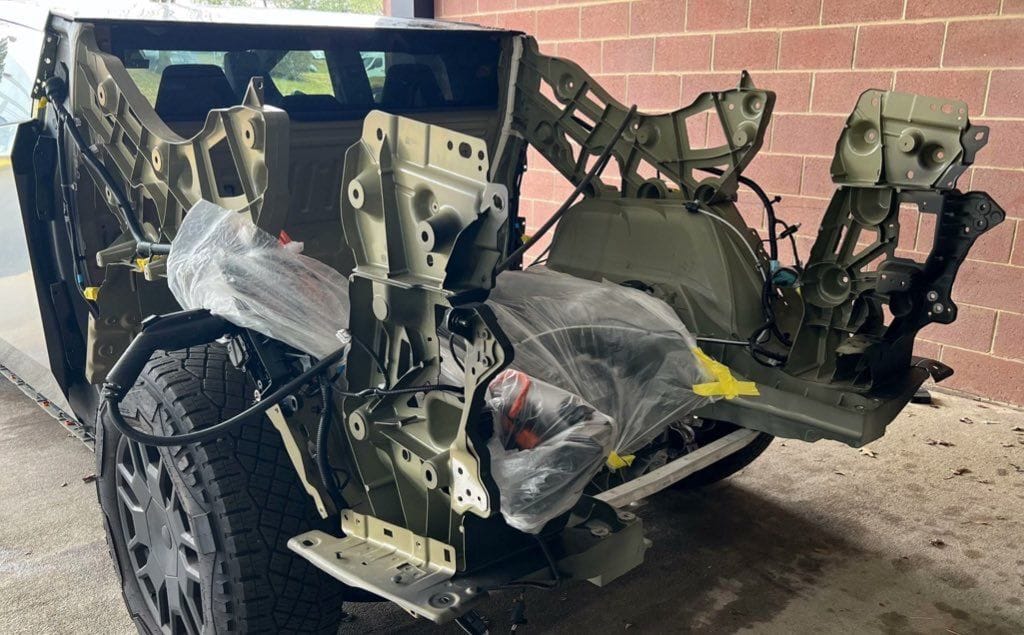
Cybertruck Rear Bed Aluminum Castings. Source Unknown